Supply chain management is the handling of the entire production flow of a good or service starting from the raw components all the way to delivering the final product to the consumer. For Re-sellers Wholesale Buyers Only.
Supply Chain Management Procedures Process Street
Supply Chain Management SCM is the systemic strategic coordination of the traditional business functions within a particular company and across businesses within.
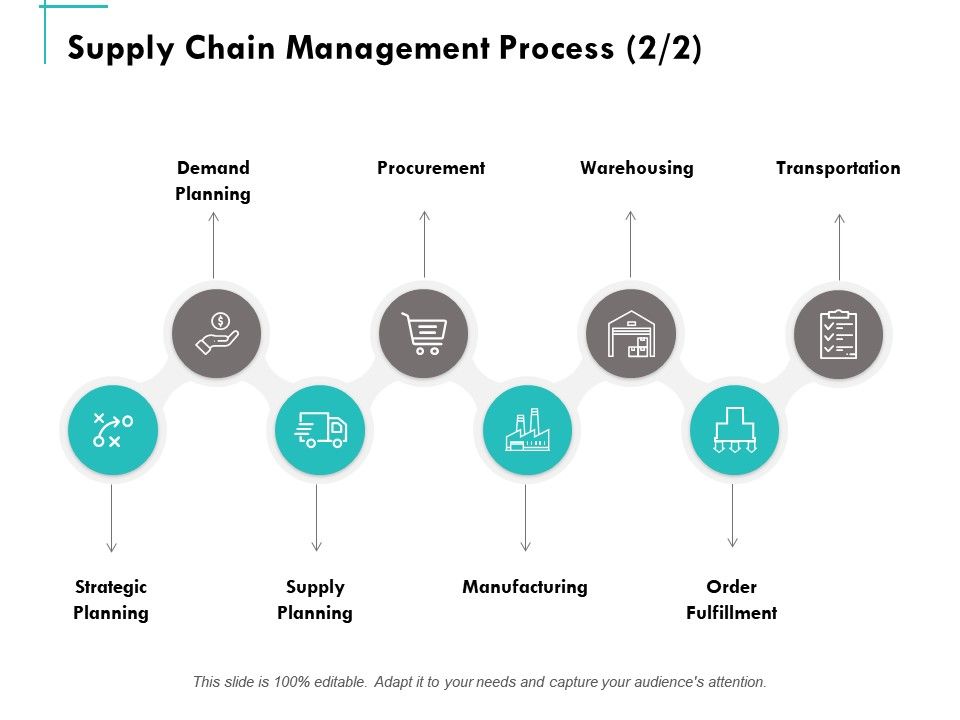
Supply chain management process. Customer Relationship Management Customer Service Management Demand Management Order Fulfillment Manufacturing Flow Management Procurement Product Development and Commercialization Returns. Business material has a journey as it moves from one state to the next until its ready to be delivered to the customer or stakeholder. Supply chain management is the management of the flow of goods and services and includes all processes that transform raw materials into final products.
Ad Download Supply Chain Management Industry Reports on 180 countries. Supply chain management can be defined as the management of the flow of products and services which starts from the origin of the products and ends with the consumption of the product. SUPPLY CHAIN MANAGEMENT PROCESS Supply chain lebih sering digunakan pada perusahaan berbasis service dan manufacturing meskipun dalam menjalankan supply chain masih sering terjadi kendala antara industry dengan industry dan perusahaan dengan perusahaan.
It also includes the movement and storage of raw materials involved. It involves the active streamlining of a. A supply chain is the collection of steps that a company takes to transform raw materials into a final product.
Supply chain management SCM is the discipline that manages supplies and processes through all of the stages of a project product or business deliverable. Instant industry overview Market sizing forecast key players trends. SCM is the oversight of materials finances and information when they move from the supplier to manufacturer to wholesaler to retailer and finally to the consumer through a predefined process.
Process in order to reduce time to market. Supply chain managers should be fully equipped with modern IT tools to keep a track on warehousing networks inventory models as well as invoicing and payment receipts. RETURN Returns handling is the last step of the supply chain management process.
It includes supply planning product planning demand planning sales and operations planning and supply management. What is supply chain management. Supply chain management is the process of delivering a product from raw material to the consumer.
In order to understand business functions supply chain management SCM is critical. Your Satisfaction is Guaranteed. Instant industry overview Market sizing forecast key players trends.
Supply chain management operations govern the overall structure of how a business plans creates receives and fulfills products. Ad Buy Quality Beautiful Trendy 925 Silver Jewelry Shipped from our Thailand Factory and Save. Ad Download Supply Chain Management Industry Reports on 180 countries.
Perbedaan proses dalam supply chain juga bisa berdampak pada customer. Supply chain management SCM is the process and activitity of sourcing the raw materials or components an enterprise needs to. For Re-sellers Wholesale Buyers Only.
Suppliers 35 into the product development. Includes integrating customers 34 and. Ad Buy Quality Beautiful Trendy 925 Silver Jewelry Shipped from our Thailand Factory and Save.
Supply chain management is a process used by companies to ensure that their supply chain is efficient and cost-effective. Why supply chain management is Important A positive or negative impact on the supply chain resounds throughout the business. Supply Chain Management The Global Supply Chain Forum identified eight key processes that make up the core of supply chain management 5.
Often referred to as OSCM operations and supply chain management it involves monitoring maintaining and improving a wide spectrum of. Your Satisfaction is Guaranteed. It not only involves reviewing returned products for quality purposes but also managing.